The atmospheric-pressure reduction unit is a general term for both atmospheric distillation and vacuum distillation. Since the two units are usually together, they are called atmospheric and vacuum units. It mainly includes three processes: desalination and dehydration of crude oil; atmospheric distillation; vacuum distillation
The main equipments of the atmospheric and vacuum installations are: towers and furnaces.
The tower is the core of the process of the entire plant. The crude oil is subjected to fractional distillation through mass transfer and heat transfer in the fractionation tower, and finally the crude oil is separated into products with different components. The most common process for atmospheric and vacuum installations is a three-stage gasification process, or “two-furnace and three-column process,” and the columns in atmospheric and vacuum columns include: a primary distillation tower or a flash distillation tower, an atmospheric tower, and a vacuum tower.
1) The atmospheric tower is a compound tower Crude oil is cut into four or five product fractions such as gasoline, kerosene, light diesel oil, heavy diesel oil and heavy oil by atmospheric distillation.
2) The raw materials and products of the atmospheric tower are all composed of complex mixtures. Crude oils can be distillated at atmospheric pressure to obtain fractions with different boiling points. For example, light distillate oils and atmospheric heavy oils such as gasoline, kerosene, and diesel oil are still complex. The mixture (its quality is controlled by some quality standards. For example, the dry point of the gasoline distillation range cannot be higher than 205°C). 35°C~150°C is naphtha or reforming raw material, 130°C~250°C is a kerosene fraction, 250°C~300°C is a diesel fraction, and 300°C~350°C is a heavy diesel fraction and can be used as a feedstock for catalytic cracking. . >350°C is atmospheric heavy oil.
3) The stripping section and the stripping column often do not have a reboiler on the bottom of the petroleum distillation column and stripping section, because the bottom temperature is relatively high, generally around 350°C. Under such a high temperature, it is difficult to find a suitable one. The reboiler heat source, therefore, usually a small amount of superheated steam blown into the bottom, in order to reduce the partial pressure of oil vapor in the tower, so that the light components mixed into the bottom of heavy oil vaporization, this method is called stripping.
Vacuum evacuation equipment for a vacuum tower is usually a steam ejector or a mechanical vacuum pump. Among them, mechanical vacuum pumps are used only in some vacuum decompression distillation towers and vacuum towers of small refineries, and steam injectors are widely used.
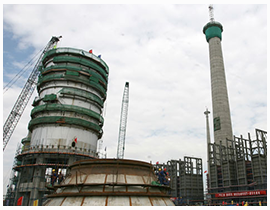
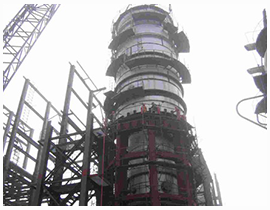
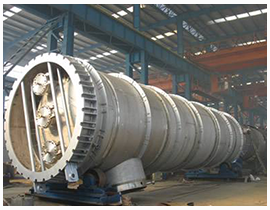
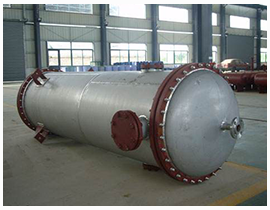
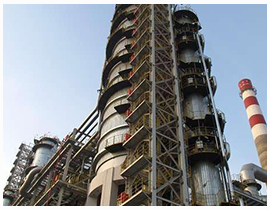
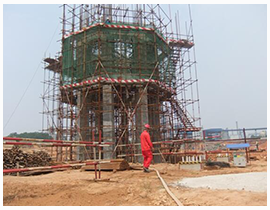
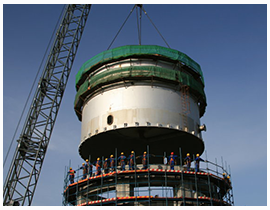
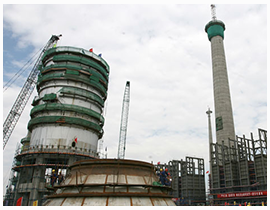
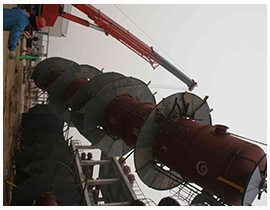
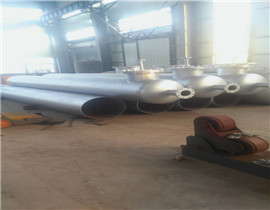
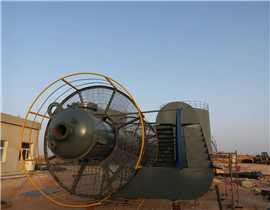
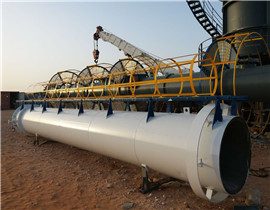
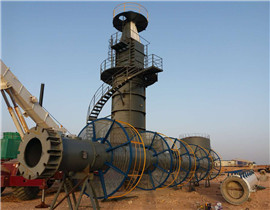
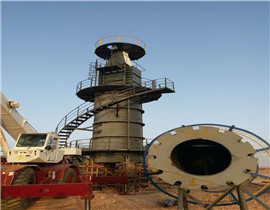